How to Reduce Costs While Maximizing Pallet Load Efficiency
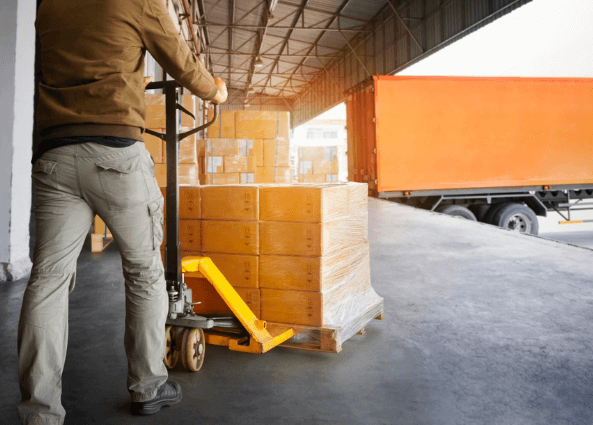
In today’s competitive business landscape, efficiency is key to maintaining profitability. One area where companies can significantly reduce costs while maximizing their operational capacity is through pallet optimization. By strategically planning how products are loaded onto pallets, businesses can minimize shipping expenses, maximize storage space, and enhance overall supply chain efficiency. This article delves into the benefits of pallet optimization and offers practical tips for achieving it effectively.
Understanding the Importance of Pallet Optimization
Pallets are a staple in logistics and supply chain management. They serve as the foundation for transporting goods, enabling easy handling and storage. However, improper palletization can lead to wasted space, increased transportation costs, and even product damage. Effective palletization not only enhances product stability during transit but also allows for better use of storage space. By optimizing pallet loads, companies can not only enhance their bottom line but also improve their sustainability efforts by reducing the number of shipments required.
One of the primary goals of pallet optimization is to maximize load efficiency. This involves strategically arranging products on a pallet to utilize every inch of space available. When pallets are packed efficiently, businesses can transport more goods in fewer trips, resulting in lower fuel costs and reduced carbon emissions. This dual benefit of financial and environmental savings makes pallet optimization an essential practice for modern businesses.
See also: Effective Strategies for Simple Financial Growth
Assessing Your Current Palletization Practices
Before implementing any optimization strategies, it’s crucial to assess your current palletization practices. Take the time to analyze how products are currently loaded onto pallets. Are there recurring issues such as wasted space or damaged goods? Gathering data on your loading processes will provide valuable insights into areas that need improvement.
Consider using tools like load optimization software, which can simulate various pallet configurations to identify the most efficient arrangements. These tools can also provide visual representations of how different products fit together, making it easier to visualize the best approach. By understanding your current practices, you can make informed decisions that drive improvements.
Standardizing Pallet Sizes and Configurations
One effective strategy for optimizing pallets is to standardize pallet sizes and configurations across your operations. Using uniform pallets can simplify loading and unloading processes, making it easier for workers to handle products efficiently. Standardization also ensures that pallets can be stacked effectively, reducing the risk of instability during transportation.
When selecting pallet sizes, consider the dimensions of your products and the transportation methods you use. For instance, if your goods are primarily shipped in containers, using pallets that fit snugly within those containers can maximize space utilization. Standardizing configurations, such as the orientation of boxes or pallets, can also streamline operations and reduce loading times.
Training Employees on Best Practices
Even the best pallet optimization strategies can fall flat without proper employee training. Ensure that your team understands the importance of palletization and the techniques for achieving optimal loads. Conduct training sessions that cover best practices for packing, stacking, and securing products on pallets.
Encouraging a culture of efficiency among employees is essential. Workers should feel empowered to suggest improvements and share insights from their daily experiences. By fostering open communication and collaboration, businesses can identify innovative solutions to pallet optimization challenges.
Implementing Advanced Technology
Incorporating technology into your palletization processes can further enhance efficiency. Automated palletizers, for example, can handle the loading process with precision, reducing the risk of human error. These machines can be programmed to load pallets based on predefined configurations, ensuring that each load is optimized for weight distribution and stability.
Additionally, consider using barcode scanners and RFID technology to track inventory as it moves through your supply chain. This technology can help monitor the condition of products during transport, allowing for timely interventions if issues arise. By leveraging advanced technology, businesses can not only improve their palletization processes but also gain valuable data to inform future optimization efforts.
Measuring Success and Continuous Improvement
Pallet optimization is not a one-time task; it requires ongoing assessment and adjustment. After implementing changes, measure the impact of your optimization strategies. Track metrics such as shipping costs, product damage rates, and loading times to evaluate the effectiveness of your initiatives.
Use this data to refine your practices continually. Regularly revisit your palletization processes to identify new areas for improvement. By committing to a culture of continuous improvement, businesses can stay ahead of industry trends and maintain a competitive edge.
Powerful Optimization Strategy
Pallet optimization is a powerful strategy for reducing costs and maximizing load efficiency in today’s fast-paced business environment. By understanding the importance of efficient palletization, assessing current practices, standardizing configurations, training employees, incorporating technology, and committing to continuous improvement, businesses can achieve significant benefits. As companies strive to enhance their operational efficiency, pallet optimization will play a vital role in ensuring sustainability and profitability for years to come. Embrace these strategies, and watch your business thrive!